A Tour of 64 Audio HQ (with Volür impressions!)
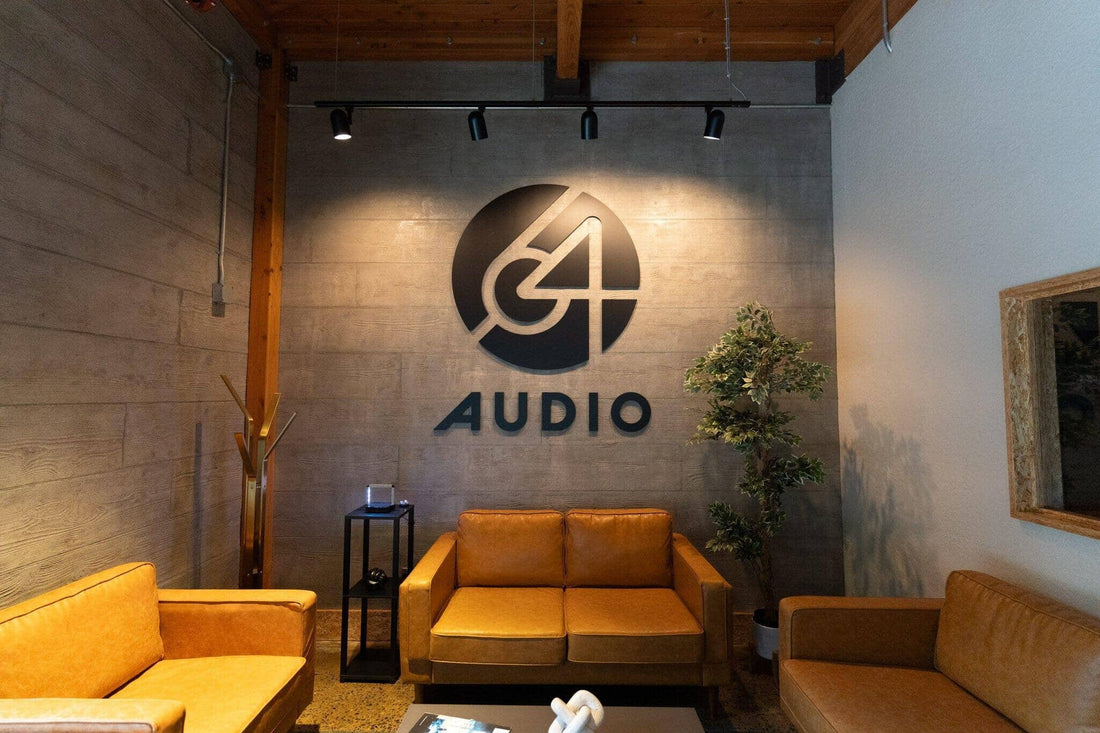
Why 64 Audio?
Perhaps another question for context: were you a good student? I’d like to think I was and, even if my teachers may have never explicitly said it, there were a lot of hints at me being a pupil that they particularly enjoyed teaching. As a reviewer, I confess that I share a similar sentiment when it comes to 64 Audio. I’ve listened to over three hundred IEMs, yet few have made an impression on me as powerful as this brand’s IEMs.
In fact, my first flagship IEM was the 64 Audio U12t which I enjoyed for over three years. Even if the U12t didn’t initially blow me away, my appreciation for it only mounted as the years passed and I got my ears on more IEMs. It consistently established itself as being a step ahead of the competition. In some sense, it’s an IEM that aged like fine wine and that curated my current sound preferences.
It stands that I’m always eager to get a listen of 64 Audio’s new products even if they haven’t always measured up to the U12t’s incredible legacy. I’ve also increasingly found my curiosity piqued by the actual development that goes behind the finished products. So when I had the chance to do an HQ tour of 64 Audio’s headquarters in Vancouver, WA, unsurprisingly, I jumped on the opportunity.
A Key Word
64 Audio’s headquarters resides in an unassuming building shortly across the bridge from Portland, OR to Vancouver, WA. Open the door and walk into the lobby, though, and you instantly know you’re in the right place thanks to the massive logo on the wall and the curated decor. A further glimpse past the lobby begins to reveal the true scale of the operation: a plethora of side rooms, row upon row of assembly stations, and a similarly packed second floor. With Filipp Skylarov (64 Audio’s head of marketing) as my guide, I was treated to an extensive tour of the facility. Frankly, I saw far too much for me to cover in full (much less remember!), but let’s dive into the highlights.
In an industry where copy-and-pasting ideas and an omnipresent race to the bottom has become the status quo, one word still comes to mind when visiting 64 Audio’s HQ: innovation. The brand is a pioneer in the professional music industry, so perhaps it should come as no surprise that they are often forced to challenge themselves and create novel solutions. Interestingly, some of the most impressive examples that I saw were not directly related to the sound of the IEMs specifically, but the manufacturing process.
A prime example is a custom Python sorting algorithm, designed by Vitaliy G. (64 Audio’s chief of research and development), for drivers. It represents an interesting insight into the idea of accuracy versus consistency. In every batch of drivers, there is some level of variation that occurs between each drivers’ frequency responses. Manufacturers have discretion over how much this can deviate from a golden sample (a sample that has the intended tuning), but ultimately, it usually makes more sense to aim for channel matching (consistency) than it does 1:1 adherence (accuracy) to the golden sample’s frequency response. This is especially true when it comes to a larger scale operation like 64A’s.
All this to say that sorting through these drivers can be a real headache, which is where this algorithm comes in. It takes a text file of drivers that have been measured and works to find ideal pairs, ranking each pair with a quality score. Drivers that don’t find a match, or fail to score adequately, can be discarded. This streamlines the process of finding matched pairs between the drivers, and it’s an ingenious process improvement that increases in value as the scale of an operation grows. It’s also a great reminder that many process improvements can be software facing, not necessarily hardware facing, even in a very hands-on manufacturing process like building IEMs.
But if we’re talking about hardware innovation, there’s plenty where that came from too. If you’re someone who swaps between cables on IEMs often, then you’ve probably realized that the sockets wear out over time. Manufacturers often have a rated socket life for the number of actuations. But what if you’re 64 Audio and take matters into your own hands with a custom socket? You also build your own machine from scratch to measure the number of connector actuations.
And ever tried measuring a CIEM? Let me tell you from experience that it is not easy because CIEMs don’t have tips to make a seal with the measurement coupler. Conventionally, measuring CIEMs is done using putty which means that 1) achieving a seal is often quite difficult and 2) achieving repeatable results might as well be impossible. 64 Audio has managed to work around this by designing their own, custom attachment for the measurement coupler. It ensures consistency and streamlines the otherwise arduous process.
Humble Beginnings
Although I got to see no shortage of cool gadgets, workstations, innovations, and even some cool prototypes like above, my visit to 64 Audio HQ was ultimately focused on the people. I had the exclusive opportunity to interview the Vitalys: Vitaly B. (owner and CEO) and Vitaly G. (chief of research and development).
I will disclaim that audio is a hobby that often delves into pseudoscience; I have found that not all manufacturers are created equal when it comes to explaining their thought processes. But from my conversation with Vitaliy G, 64 Audio’s chief of research and development, 64 Audio seems to fall on the more sober end of the spectrum.
His stance on burn-in was one that particularly surprised me: he believes that the first ten seconds or so of listening are the most important. You shouldn’t be forcing your ears to acclimate to a set; you want a set that almost instantly sounds natural to you. Logically this makes sense, but it was particularly refreshing to hear given that manufacturers have nothing to lose by suggesting consumers just keep listening longer for that “ah-ha” moment. I also enjoyed his stance on driver count: the amount of drivers doesn’t matter. He presented an apt real-world analogy. Drivers work like a sports team; if someone isn’t being a team player, or the players don’t know how to coordinate, then it can be a detriment more than a benefit.
Me being me, I did ask some more…shall we say, spicy questions. One of the most humbling answers I got was when I asked Vitaly B. about 64 Audio’s stance on increased competition thanks to Chi-Fi. It’s no secret that getting good sound is no longer the luxury it once was, as there are even many sub-$50 IEMs that sound reasonably good. The bottom line? According to him, they have been caught off guard, they have been feeling the heat, and they do need to step up their game. More on that later.
I’ve also always been curious about the sales breakdown between CIEMs (custom in-ears) and UIEMs (universal in-ears). How can they cost the same when CIEMs seem much more involved? Is it simply economies of scale? One part of the equation: 60/40 CIEMs. But the main reason that they are priced equally is that working with CNC aluminum for the UIEMs is a less forgiving process than 3D printing for the CIEMs. An added benefit of equal pricing is that it allows consumers to disregard price and to choose based on their needs.
Listening Impressions from the Demo Room
No HQ visit would be complete without listening to some actual products. And in this case, I had access to all the products. 64 Audio even had a dedicated listening room near the front lobby of the building, complete with decked-out listening stations that I took advantage of for a couple hours.
First, I had an opportunity to hear an prototype, called the Volur, that is going to be the second version of the Nio. If the Nio is more L-shaped (strongly bass focused and darker up top) then the Volur is more V-shaped. It adds back in a lot of the mid-treble and upper-treble that is missing on the Nio, and it also seems to emphasize the 3kHz region slightly more. In general, bass notes come across sharper and more controlled on the Volur; however, it does not have the incredible decay that the original Nio’s bass has. I suspect that they have a similar quantity of bass, though, and that this perception is mostly a product of the Volur's stronger treble focus. In general, the Volur cranks things up across the board: it is a more lively rendition of the Nio that is reminiscent of the Trio in some respects, especially in the treble. I would say that its technical performance is also commensurate with the Trio. It surpasses the Trio for a sense of dynamics, but it does not match the Trio’s imaging due to the Trio’s unique 1kHz recession and extra space between treble peaks.
The first time I heard the U3t (the A3t demo) was at CanJam; while I didn’t have as much time with it as I’d have liked, I was immediately impressed. A closer listen in the optimal conditions of 64 Audio’s demo studio only confirmed these impressions. Tonally, the U3t is about 90% of the U12t; it absolutely nails the skeleton of the U12t’s winning formula. The distinction rests in technicalities of course. The U12t has extra presence in the sub-bass and upper-treble which results in more contrast across the frequency spectrum; therefore, an increased sense of resolution and dynamics. I also found that the U12t’s upper-midrange is pulled back slightly more for increased center imaging. All around, the U3t is a warmer, smoother listen. It is impressive to me that the U3t achieves slightly-less-than-comparable performance to the U12t at a fraction of the driver count. In some sense, I think it could be considered the ‘essence’ of 64 Audio’s house sound; rest assured I would be highly tempted to add it to my stable if a universal version is released.
Comparatively, there is not much to say about the A3e. The A3e is more or less the A3t with the tia driver stripped out for a standard BA. In some sense, I think that the A3e illustrates the pivotal role that the tia driver plays in the tuning of 64 Audio’s IEMs. It seems integral to pulling off the more recessed upper-midrange that their IEMs tend to sport. Generally, I don’t think the A3e is very impressive; it’s inoffensive, but it certainly wouldn't be my first pick at its price point. And I have even less to say about the A2e. The A2e is a dead-ringer for low-driver count stereotypes. It has more of a mid-bass focus than the A3e/A3t, and its upper-midrange is extremely recessed. Stack on poor treble extension and you get a hazy, uninspiring listen.
Despite my less than thrilling comments about some of these IEMs, the landscape of the IEM market has become increasingly homogenous - many IEMs sound quite similar. 64 Audio is one of the few companies that hasn’t been afraid to stick to their guns and embrace alternative styles of tuning which is one reason why I’ve enjoyed their products in the past.
Wrap-Up
Aside from the 64 audio’s latest release, the question is always what’s next from the brand? First, straight from 64 Audio themselves, they recognize that they are not the fastest moving brand. They would prefer to take their time, and they want it to be something that shifts the paradigm when they release a product. In fact, there have been a lot of products in the works that simply haven’t made it to fruition (including a TWS IEM!). Nonetheless, they have seen there is concentrated demand at both the lower ends and the higher ends of the market, so they are looking at stretching the rubber band in future releases.
Overall, my visit to 64A lent an interesting ‘flip the script’ perspective. As consumers, it’s common to only see the end product; as a reviewer, it’s even easier for me to tear something down in a review. But I think there’s an interesting parallel to not understanding what’s going on in someone else’s life unless you’ve actually been in their shoes. While I certainly won’t go so far as to say I achieved this parallel, I feel like I got a glimpse into what it’s actually like behind the helm. Ultimately, there are not only a ton of wonderful folks putting in work on 64A’s products, but there’s also a myriad of considerations that go into releasing the end products that we might not always recognize.